
o b t a i n i u m Inc.
In spite of the limitations in creating a wide palette of functionally graded materials, this technology remains one of hotly researched field within 3D Printing and hold possibility of creating a new design paradigm.
The research we conducted at NCSU around 2003-2005 lead to the development of additively manufactured non-stochastic foams; also referred to as lattice structures. In simple words, we demonstrated the parts whose insides were made out of repeating lattice structures (figure below). Additionally, the shape, size and configuration of the lattice structures could be gradually changed any where over the geometry of the part. This translated into the ability to vary part properties across the part without varying the part material: a major barrier in achieving functional gradients was thus broken.
With control over over porosity and structure of the pores, we could design parts with physical properties that were orders of magnitude different from the material they were made of. A part could be more flexible more flexible than the material they were made up of. More efficient heat exchangers could be designed without compromising on flow efficiency. Additionally, functional gradients could be build by varying porosity or structure of the pores across the part.
Figures below show non-stochastic foams. The bottom-left figure shows a titanium alloy Ti-6Al-4V foam with functional gradients. The bottom-right figure shows a non-stochastic foam made via stereolithography. The lattice structure of this foam exhibits negative Poisson’s behavior, a property rarely found in nature. This foam has a very unique behavior. Typically when we press upon naturally occurring substrances in one direction they expand in another. The material is said to possess a positive Poisson’s ration. The foam in the picture has negative Poisson’s behavior, meaning, if it is compressed in one direction, the foam will compress in other directions as well. Not only is this an unusual behavior, but the behavior of the foam can be finely programmed.
The concept of 3D Printed lattice material was rapidly explored by both research and industry. Today we can see the evidence through both the incorporation of this technology in commercial products and number of research papers published on this topic. To truly harness the capabilities of lattice based parts, it was important to design them in CAD so the parts could be manufactured using a computer controlled 3D Printer. Conventional CAD software are not optimized to handle such complexity and would end up crashing in no time.
Consider a simple lattice structure, 1mm cube in size with 8 beams. Once this structure is populated into a part that is 70mmx70mmx70mm, we are looking at 8x70x70x70, which is over 2.7 million entities. The beams are made of points, edges and facets, so this further increases the number of individual entities. Conventional mechanical CAD softwares are not designed to handle such complexity and end up crashing. Additionally, the conventional CAD methodology to developing lattice structures used boolean operations that resulted rogue artificats in the lattice structures that were prone to locally fail during loading.
Immediately after conducting initial research on lattice materials, we saw the commercial potential for this technology. The hindrance to realization of lattice material based lied in lack of specialized CAD design tools. Obtainium developed CAD design tools specifically for the design of clean, optimized lattice structures based parts. The figure below shows a 3D CAD model populated with lattice structures using software tools I developed. Both stand alone lattice tools and plugins into commercial CAD packages were developed. More recently, we have seen commercial lattice design tools by other vendors: NetFabb GmbH, Within Labs (accquired by Autodesk), Paramount Industries (accquired by 3D Systems).


Lattice structures mase using EBM 3D Printing process in titanium alloy Ti6Al4V
Lattice structures exhbiting negative Poisson's ration produced via Sterolithography 3D Printing process


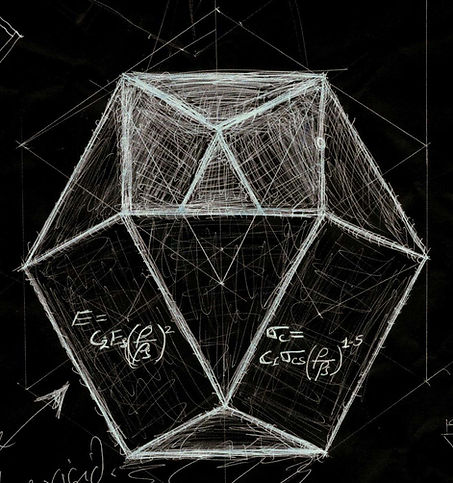
Obtainium Inc. developed tools for the design of functionally graded lattice based materials to extend 3D Printing capabilities to print parts with tuned properties.
Since the advent of 3D Printing, researchers have pursued developing capabilities of printing multiple materials within the same part. The idea held the promise of making parts with amazing properties; conducting on one side insulating on another, planes where regions were dense and strong in certain regions and light in non load bearing regions. Think of the promise such technology held. The challenge was that, though materials of different composition could precisely be deposited at a given point in space, the materials may not be compatible with one another. The materials have largely differing melting points and thermal expansion coefficients or they may even have completely non-compatible chemistries. This limitation has been a challenge in realization of what are called freeform functionally graded materials.
3D CAD Model populated with lattice structures